XYFL-20, 20HP के मुख्य पैरामीटरएयर-कूल्ड चिलर:
प्रशीतन क्षमता: 60KW, कंप्रेसर पावर: 20HP/15KW, वोल्टेज आवृत्ति: 3PH-380V-50HZ (आप विभिन्न देशों के अनुसार वोल्टेज आवृत्ति को अनुकूलित करने के लिए ग्राहक सेवा से परामर्श कर सकते हैं), कंप्रेसर ब्रांड: पैनासोनिक, पानी की टंकी की क्षमता: 245L, बाष्पीकरणकर्ता संरचना: प्लेट ट्यूब प्रकार, कंडेनसर संरचना: फिन प्रकार, जल पंप शक्ति: 1500W, रेफ्रिजरेंट मॉडल: R22 (आप पर्यावरण के अनुकूल रेफ्रिजरेंट को अनुकूलित करने के लिए ग्राहक सेवा से परामर्श कर सकते हैं), इनलेट और आउटलेट व्यास: DN50, वजन 850KG।
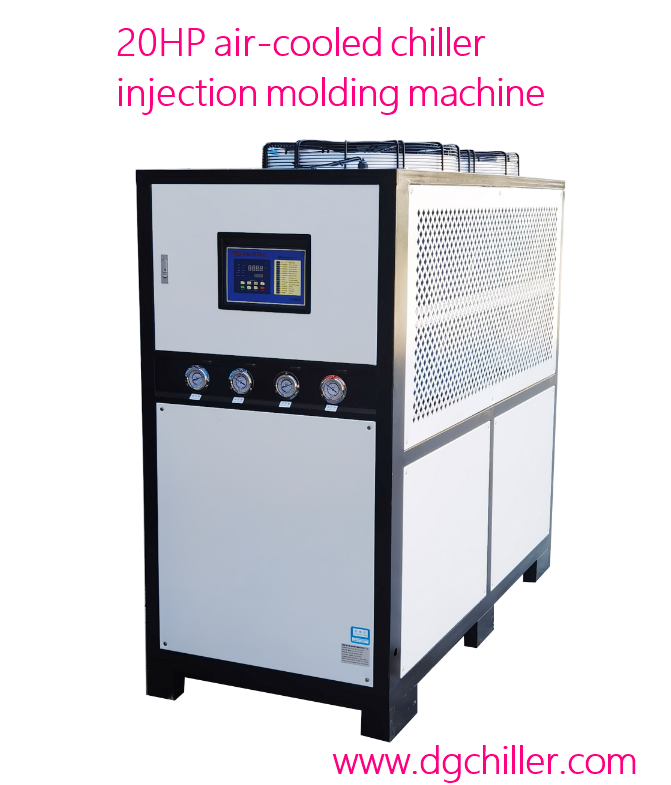
मानक इंजेक्शन मोल्डिंग मशीन के लिए वाटर-कूल्ड चिलर का चयन करने की विधि निम्नलिखित है:
जब इंजेक्शन मोल्डिंग मशीन के ठंडा पानी का तापमान 5-10 डिग्री सेल्सियस पर नियंत्रित किया जाता है, तो 1HP शीतलन क्षमता वाले चिलर का मिलान 80T से किया जाता है।
जब इंजेक्शन मोल्डिंग मशीन के ठंडा पानी का तापमान 10-15 डिग्री सेल्सियस पर नियंत्रित किया जाता है, तो 1HP शीतलन क्षमता वाले चिलर का 100T से मिलान किया जाता है।
जब इंजेक्शन मोल्डिंग मशीन के ठंडा पानी का तापमान 15-20 डिग्री सेल्सियस पर नियंत्रित किया जाता है, तो 1HP शीतलन क्षमता चिलर 120T के साथ मेल खाता है।
मानक इंजेक्शन मोल्डिंग मशीन वैकल्पिकएयर-कूल्ड चिलरतरीका:
जब इंजेक्शन मोल्डिंग मशीन के ठंडा पानी का तापमान 5-10 डिग्री सेल्सियस पर नियंत्रित किया जाता है, तो 1HP शीतलन क्षमता वाले चिलर का मिलान 64T से किया जाता है।
जब इंजेक्शन मोल्डिंग मशीन के ठंडा पानी का तापमान 10-15 डिग्री सेल्सियस पर नियंत्रित किया जाता है, तो 1HP शीतलन क्षमता वाले चिलर का मिलान 80T से किया जाता है।
इंजेक्शन मोल्डिंग मशीन का ठंडा पानी का तापमान 15-20 डिग्री सेल्सियस पर नियंत्रित किया जाता है, और 1HP शीतलन क्षमता चिलर 96T के साथ मेल खाता है।

XYSL-20, 20HP वाटर-कूल्ड चिलर कोर पैरामीटर:
प्रशीतन क्षमता: 60KW, कंप्रेसर पावर: 20HP/7.5KW, वोल्टेज आवृत्ति: 3PH-380V-50HZ (आप विभिन्न देशों के अनुसार वोल्टेज आवृत्ति को अनुकूलित करने के लिए ग्राहक सेवा से परामर्श कर सकते हैं), कंप्रेसर ब्रांड: पैनासोनिक, पानी की टंकी की क्षमता: 220L, बाष्पीकरणकर्ता संरचना : कुंडल प्रकार, कंडेनसर संरचना: शेल और ट्यूब प्रकार, जल पंप शक्ति: 1500W, रेफ्रिजरेंट मॉडल: R22 (आप पर्यावरण के अनुकूल रेफ्रिजरेंट को अनुकूलित करने के लिए ग्राहक सेवा से परामर्श कर सकते हैं), इनलेट और आउटलेट व्यास: DN50, वजन 720KG।
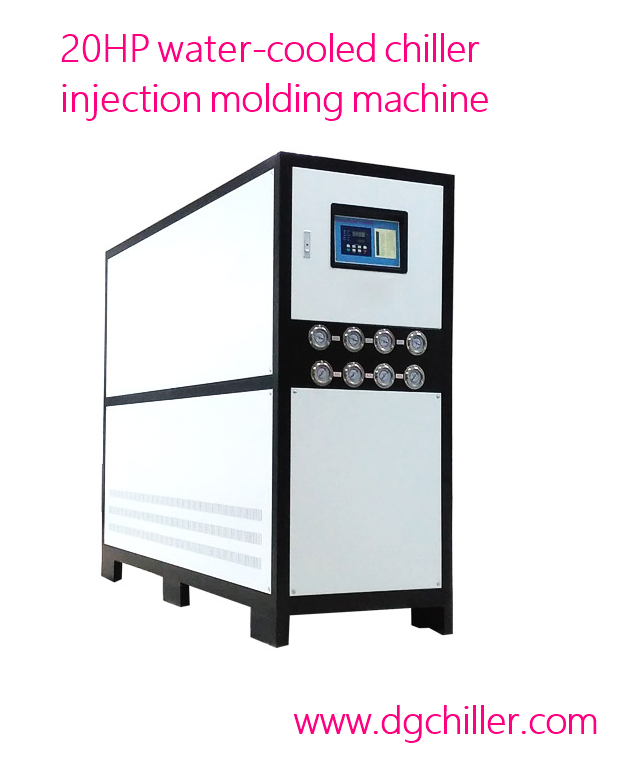
मानक इंजेक्शन मोल्डिंग मशीन की विशेषताएं: हाइड्रोलिक पंप मोटर का उपयोग किया जाता है, मोल्डिंग गति औसत है, मोल्डिंग का समय लगभग 10 सेकंड है, लेकिन अधिकतम क्लैंपिंग बल कई हजार टन तक पहुंच सकता है।
हाई-स्पीड इंजेक्शन मोल्डिंग मशीन की विशेषताएं: यह तेल पंप और सर्वो मोटर की तेल-इलेक्ट्रिक हाइब्रिड शक्ति को अपनाती है, और मोल्डिंग गति तेज है। उदाहरण के लिए, मोल्डिंग का समय लगभग 6 सेकंड है, और क्लैंपिंग बल वर्तमान में 850 टन के भीतर है।
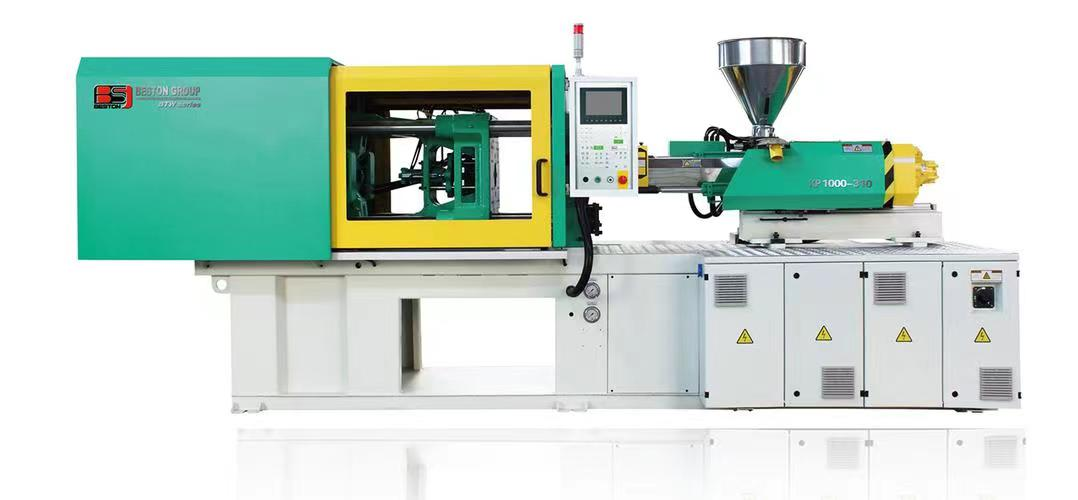
हाई-स्पीड इंजेक्शन मोल्डिंग मशीन मिलान विधि:
मानक इंजेक्शन मोल्डिंग मशीनों की तुलना में पानी की कूलिंग 0.62 गुना है, और मानक इंजेक्शन मोल्डिंग मशीनों की तुलना में एयर कूलिंग 0.55 गुना है।
हाई-स्पीड इंजेक्शन मोल्डिंग मशीन और वाटर-कूल्ड चिलर की चयन विधि:
चिलर पावर मानक 50T क्लैंपिंग बल इंजेक्शन मोल्डिंग मशीन की 1HP रेफ्रिजरेटिंग क्षमता (5-10 ℃)
चिलर पावर मानक 62T क्लैंपिंग बल इंजेक्शन मोल्डिंग मशीन की 1HP रेफ्रिजरेटिंग क्षमता (10-15 ℃)
चिलर पावर मानक 75T क्लैंपिंग बल इंजेक्शन मोल्डिंग मशीन की 1HP रेफ्रिजरेटिंग क्षमता (15-20 ℃)
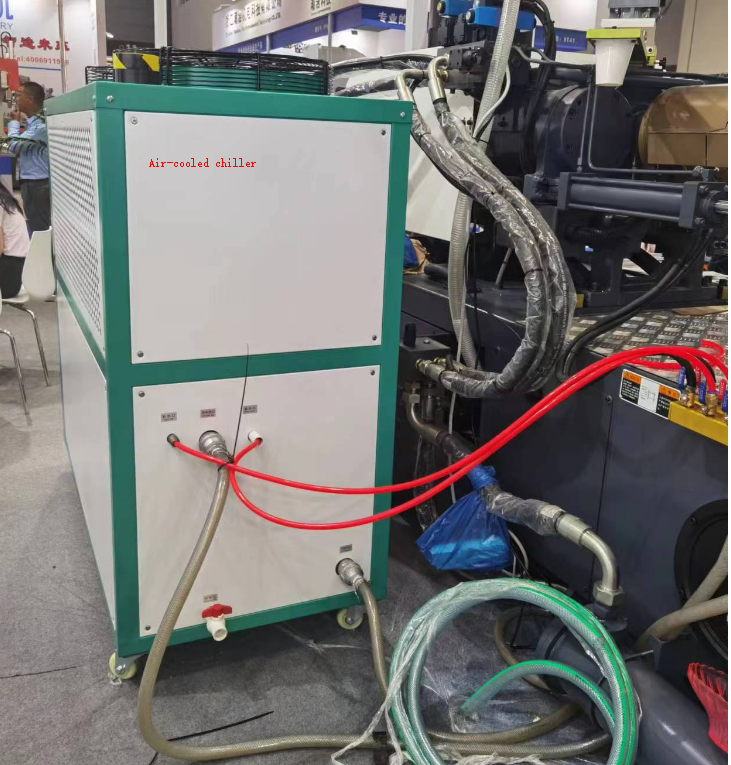
हाई-स्पीड इंजेक्शन मोल्डिंग मशीन की चयन विधि औरएयर-कूल्ड चिलर:
1HP रेफ्रिजरेटिंग क्षमता वाली चिलर पावर मानक रूप से 45T क्लैंपिंग फोर्स इंजेक्शन मोल्डिंग मशीन (5-10°C) से सुसज्जित है।
चिलर पावर मानक 55T क्लैंपिंग बल इंजेक्शन मोल्डिंग मशीन की 1HP रेफ्रिजरेटिंग क्षमता (10-15 ℃)
1HP रेफ्रिजरेटिंग क्षमता चिलर पावर मानक 66T क्लैंपिंग बल इंजेक्शन मोल्डिंग मशीन (15-20 ℃)
उदाहरण के लिए: साँचे की एक जोड़ी पीपी उत्पादों का उत्पादन करती है, और उत्पादन क्षमता 50KG प्रति घंटा है। शीतलन क्षमता कितनी आवश्यक है? हाई-स्पीड इंजेक्शन मोल्डिंग मशीन किस आकार के लिए उपयुक्त होनी चाहिए?
Q=50×0.48×200×1.35=6480 (किलो कैलोरी/घंटा)
शीतलन क्षमता 6480kcal/h प्रति घंटा है, और वैकल्पिक चिलर की शीतलन क्षमता 6480kcal/h, 6480÷860=7.5KW=3.2HP से अधिक है, इसलिए 3-5HP की शीतलन क्षमता वाला चिलर चुनें।
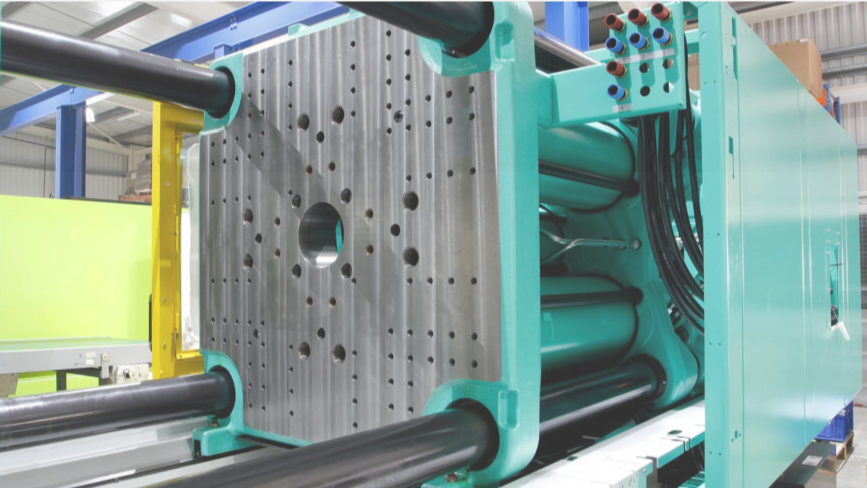
सारांश: इंजेक्शन मोल्डिंग मशीन में 20HP चिलर का मुख्य कार्य गर्म और पिघलने के बाद प्लास्टिक के कणों को मोल्ड में इंजेक्ट करना है। जमने के बाद, मोल्ड खोला जाता है और प्लास्टिक वर्कपीस को बाहर निकाल दिया जाता है। प्लास्टिक के जमाव के समय को कम करें, आयामी सटीकता, मोल्डिंग गुणवत्ता और वर्कपीस की सतह की गुणवत्ता में सुधार करें।